Hardness is one of the material properties that allows the material to resist plastic deformation. The plastic deformation may be because of penetration or in some other way. The resistance can also be from bending, scratching, abrasion or cutting etc.
Brinell Hardness Test determines the Brinell hardness. It is said for a material which has a structure very coarse or has a very rough surface to be tested using any other method. The other methods include casting and forging.
In Brinell testing, a very high testing load (about 3000 kgf) is used along with a wide indenter (10 mm). Due to this, the resulting indentation averages out most of the surface.
The test begins with applying a predetermined test load (f) to a tungsten carbide ball, having fixed diameter, for a certain amount of time. Once the load is removed, the impression is measured across at least two diameters. The two diameters are measured at right angles to each other and then averaged out. A standard chart for Brinell Hardness Test is the looked at and the averaged out diameter value is converted to a Brinell hardness number. As mentioned before, the testing force goes from 500 to 3000 kgf.
The results obtained from the Brinell hardness test method is the measurement of the width of indentation produced by the tungsten-carbide indenter which is applied to a specimen, being tested, for a certain period of time. The measurement of the indentation diameter is done using a specially designed Brinell optical system. The value obtained as the results is then converted using a formula or using a standard chart, as mentioned earlier.
While quoting a Brinell hardness number, there is a need to specify the conditions of the test also. For most of the tests, the specific load is defined as 3000 kgf on a 10 mm tungsten-carbide ball. A standard time for the testing is 10-15 seconds. However, a shorter time could be set for certain tests. The other factors that are to be considered during this tests are testing on a round specimen, minimum thickness of test specimen, spacing of indentation etc.
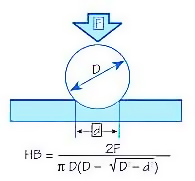
Figure 16 - Brinell Hardness
Where;
D = Ball Diameter
d = Impression Diameter
F = load
HB = Brinell Result
While performing Brinell testing, the greatest source of error that can occur is in the measurement of the indentation. The results may vary in even perfect conditions and less than that can cause great variation. The testing surface is frequently prepared to remove any surface conditions. On the other hand, the jagged edge makes the interpretation of the measurement quite difficult.
However, these errors can be eliminated or minimized using few technological techniques. The use of computers to analyze the image and read the indentations can be done using automatic optical Brinell scopes. This way, the results obtained are much accurate than from the operator's point-of-view. Another way is the measuring of Brinell hardness along with Rockwell hardness. This allows the operator to establish the correct values where an offset to the results are required.
In terms of economics, there are some elements that are to be considered. The purchase price of the device and universalism of the application. These aspects are considerable when different forms of specimen with different surface treatments are ebing tested. Other aspects include the measurement period and the qualification needed to operate the device.
No comments:
Post a Comment